Thermomechanical solder joint reliability: a physics-of-failure approach
- hookeelectronics
- Dec 10, 2024
- 1 min read
Embedded electronic equipment can operate in severe thermal environments that can damage solder joints. During temperature cycles, the Coefficient of Thermal Expansion (CTE) mismatch between components and the Printed Circuit Board (PCB) subjects solder joints to shear loading. Over time, this stress can lead to solder joint cracking, ultimately causing the failure of the electronic board.

This macroscopic thermomechanical behavior has direct implications at the microscopic level. The widely used SAC305 solder alloy, a lead-free material primarily composed of tin, recrystallizes locally during temperature cycles (creation of highly disoriented smaller grains), weakening the structure and providing a preferred path for cracking.

Observing recrystallization during failure analysis is a direct indication that solder joints are subjected to significant thermomechanical solicitations during their operational life. This observation provides crucial information about the location of thermomechanical damage, which can be used to perform finite element analysis to assess solder joint reliability.

The identified damaged volume in solder joints directly correlates with the fatigue criteria calculated in finite element analysis, such as the inelastic strain energy density shown in the figure below. This physics-of-failure approach aligns with the theory of creep rupture under cyclic loading, where the slope of the fatigue curve must equal -1. It allows for accurate lifetime predictions of SAC305 solder joints subjected to temperature cycles.
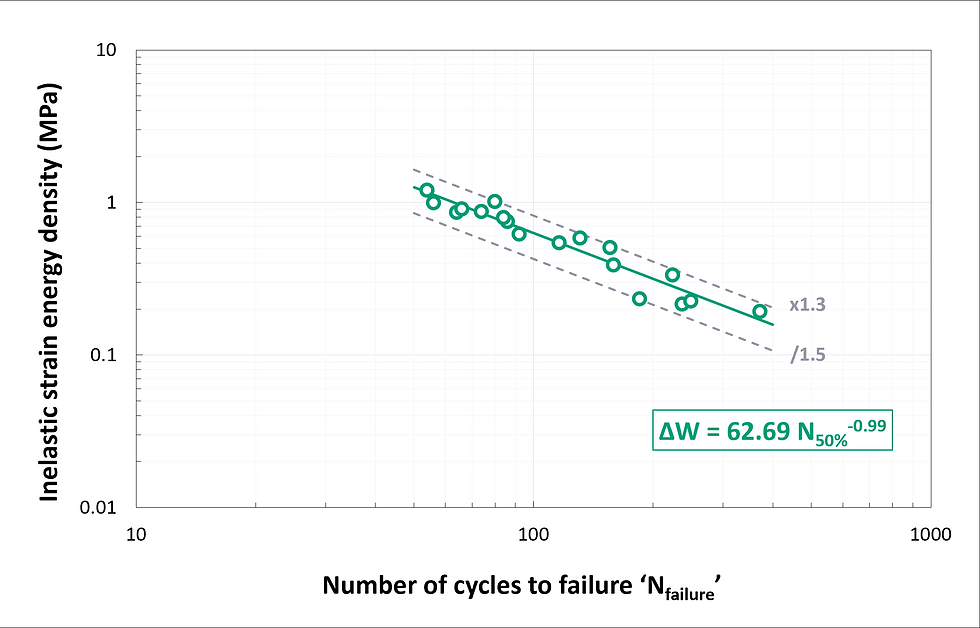
Comments